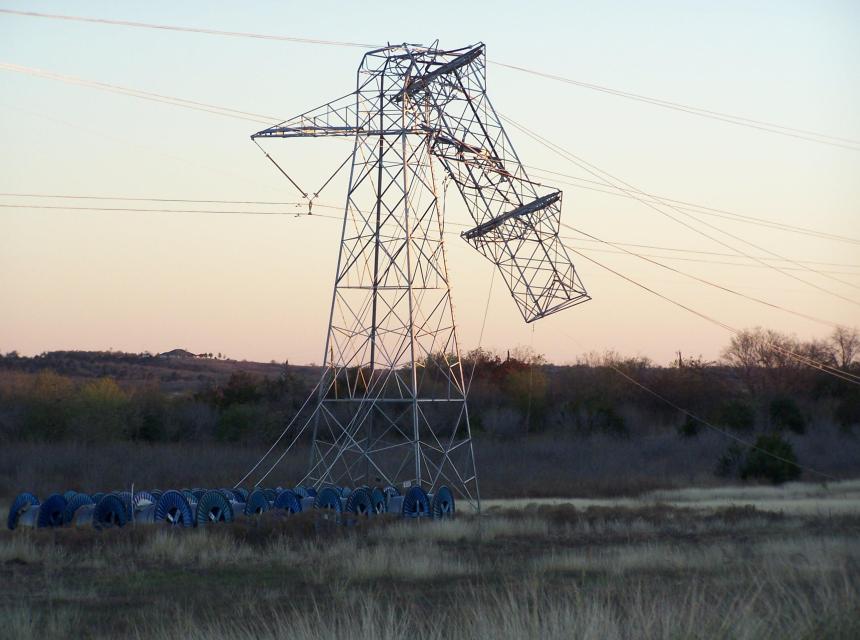
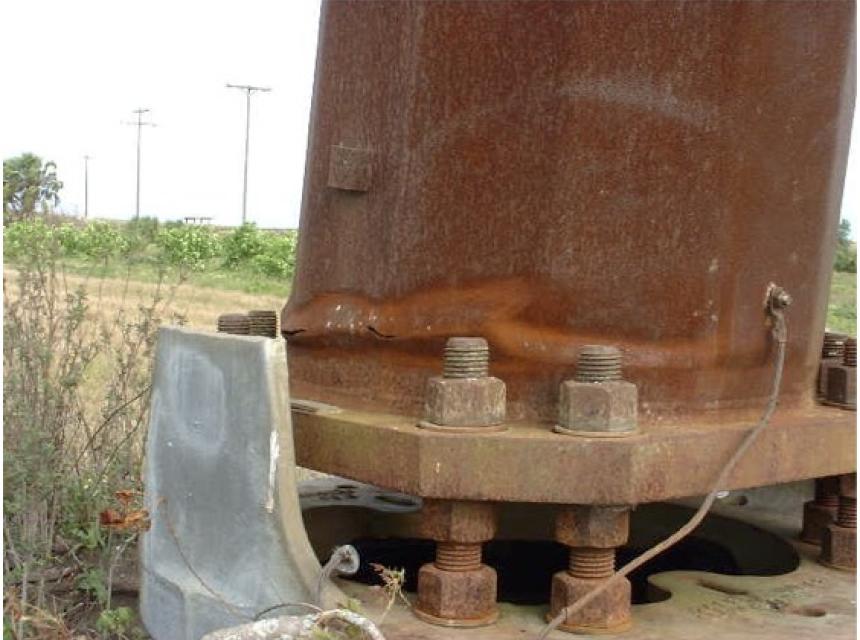
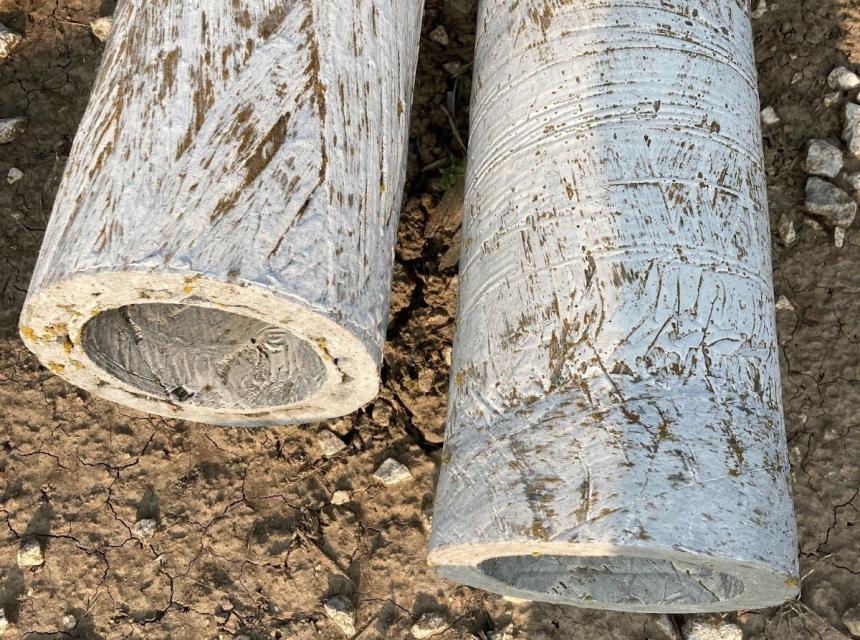
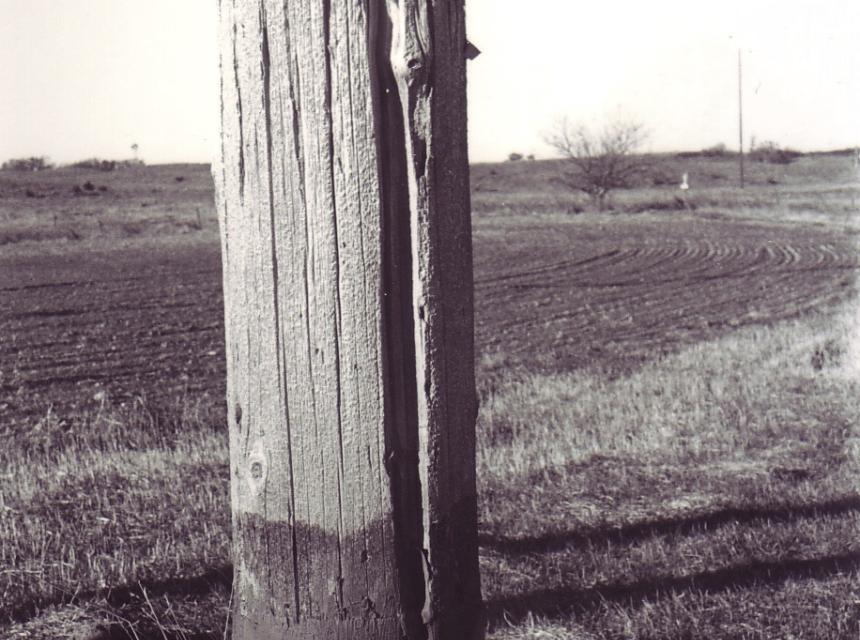
I recently accepted the inevitable: moving up to the senior tees. Given my history as a single-digit handicap golfer, this was hard on my ego. Back injuries and age made playing from the “normal” men’s tees exhausting. However, an amazing thing happened. While I no longer hit those booming drives I could at the peak of my game, my handicap moved back down. And golf was fun again!
Infrastructure is like golfing. It’s strong and resilient in the early years, but time takes a toll as it ages. Technological advancements have made the job easier, so golf courses are stretched to ridiculous lengths in response to titanium drivers and better golf balls. This is similar to how transmission lines are asked to hold larger wires and span longer distances than ever, occasionally with only one pole instead of two.
Wood poles, similar to the human body, lose strength over time. If you were 65 years old and could regain the strength you had at 25, you obviously would. That’s what utilities count on when they retire wood poles after a long service life. They replace them with newer, stronger poles to harden the grid, restoring their original strength.
Contrary to popular belief, wood is, in fact, an engineered material. I use engineering processes, no matter the material. Throughout my career, I have engineered and invented countless steel components. However, this doesn’t diminish my appreciation of a proven product, like wood, which I also design and engineer.
The term "engineered" is often mistakenly thought to be exclusive to certain materials. Regardless of the type of material used, such as wood, steel, composite fiberglass, or concrete, engineering is necessary for all poles. However, that fact is glossed over as these materials compete to replace wood poles.
It’s easy to dismiss wood poles because we’ve been using them for more than a century. Utilities continue to use them, with tens of thousands of preservative-treated wood poles installed annually. Why? Because they have a proven record of performing for many decades. They are economical and readily available. Promises of newer, stronger alternatives often neglect these enduring benefits of wood poles.
The American Society of Civil Engineers Manual of Practice No. 141 for Wood Pole Structures notes in Appendix A.4: “The use of wood pole structures, properly designed, may provide a more resilient option than other materials used.”
Resilient: adjective
1) able to withstand difficult conditions 2) able to recover quickly
Aren’t all utilities after resilient systems? Dismissing wood in favor of newer materials overlooks wood's inherent engineered quality, especially when no material lasts forever.
There are extensive records on the service life of wood poles. In some regions, it's not uncommon to find poles in service for 60-80 years or more with proper maintenance. This stands in contrast to materials like composite fiberglass, whose service life claims are based on extrapolation rather than proven performance.
For example, composite fiberglass promoters claim the service life of their poles to be 100 years or more. This is based on tests conducted according to the ASTM G151 standard for accelerated weathering. However, ASTM itself cautions: “Even though it is very tempting, calculation of an acceleration factor relating X hours of a laboratory accelerated test to Y months or years of exterior exposure is not recommended.” Since composite fiberglass poles have been available for the past 25 years, claims of 100-year service life are, at best, a guess.
Unfortunately, misleading claims about alternative materials and their superiority over wood have become more prevalent. For example, a recent article by a composite fiberglass promoter misstated information about the availability of wood poles, inferring that the US is running out of forests and, therefore, available poles. In reality, for every tree harvested, multiple new ones are planted, and U.S. Forest Service statistics confirm that timber growth exceeds harvest rates.
The notion that newer materials are required for “today’s storms” is misleading. The challenge lies in engineering overhead systems to withstand anticipated loads, achievable with various materials, including wood. Designing systems never to experience an outage, as one recent article stated, is unrealistic due to the cost; instead, we aim for resilience through engineering. Often, the easiest, most economical option is replacing older wood poles near the end of their service life with newer wood poles.
When it comes to the environment, few materials can match wood in terms of being earth-friendly. Wood poles come from a sustainable, renewable resource. Wood poles have the lowest impact out of all alternatives, documented in lifecycle assessments conducted under impartial, international standards. And wood poles sequester significant volumes of carbon, holding it in place for decades.
The rush to be cloaked as a green product often ignores some manufacturing realities. The production of alternative materials, such as steel and fiberglass, poses environmental concerns. Steel production is energy-intensive, and fiberglass fabrication emits hazardous pollutants, as noted by the U.S. Environmental Protection Agency (EPA). These pollutants include styrene, which can cause nerve and liver damage in acute exposures. That is rarely talked about.
All materials have benefits and drawbacks, so for one to claim superiority over another is often an exercise in futility. As an engineer with experience in various materials, I advocate for a balanced approach in selecting materials for poles and framing without overlooking proven options, even though on the surface, they may seem boring.
Which segues back to my golf analogy; I found that chasing the newest driver technology to get 10 or 20 more yards off the tee box was nothing more than me falling for flashy advertising. I love my older driver and putter; they generally find fairways and the bottom of the cup, which is exactly my goal. (Disclaimer: I did get fitted for new irons; I’m only human, after all).
By Larry Vandergriend, P.E., Hughes Brothers., Inc.
Larry Vandergriend, P.E, is the vice president of engineering at Hughes Bros, Inc., who has supplied wood, steel, and fiberglass to the electric utility industry since 1921. He has worked in the industry for 34 years, is a member of ASCE, IEEE, and American Wood Protection Assn., and is currently president of Western Wood Preservers Institute. Larry has published numerous articles and has been involved in many standards across the utility industry, including as a member of ASCE MOP 141. During their development, Hughes Brothers has tested over 120 full-scale transmission structures and 1,300 components for the utility industry.